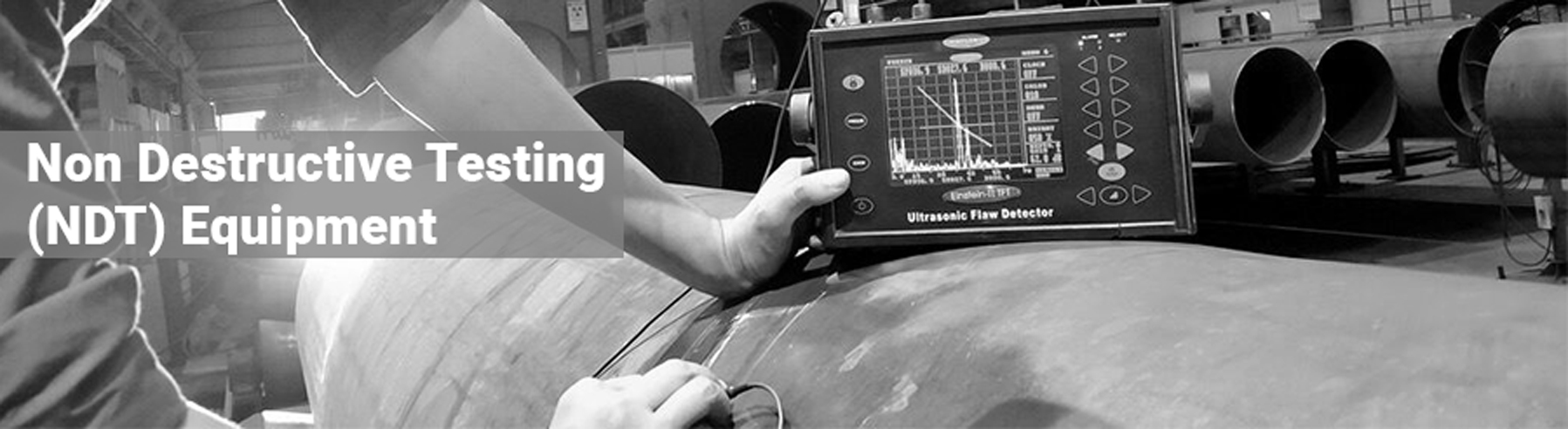
Non Destructive Testing (NDT) Equipment
Non-destructive testing (NDT) equipment is used to identify, evaluate and measure defects, bond integrity, and other material conditions without modifying or damaging the examined part or product. Many industries, especially fire and safety, use NDT to identify flaws, irregularities and to evaluate safety in equipment and assets, enhancing the product life cycle.
Many Non Destructive Testing (NDT) methods are used in the oil and gas inspection industry as it is operated in compliance with the stringent standards that primarily aim to keep equipment running smoothly while preserving workplace safety.
At H2AIM, we combine our practical experience and expertise with the latest inspection technologies to create an end-to-end testing solution for the fire and rescue industry. In the oil and gas sector, our unique NDT methods are extremely useful to inspect welds on pipelines and pressure vessels. It is also beneficial in examining non-metallic materials like concrete and ceramics.
We offer high-tech ultrasonic inspection equipment along with hardware and software solutions for special applications. Ranging from testing solutions with single and multi-channel instruments and conventional ultrasonic technology to advanced phased array, we can cater to your requirements.
Our Personalized NDT Solutions incorporate
Ultrasonic Flaw Detection
H2AIM applies Ultrasonic Flaw Detection for identifying subsurface flaws in an object using ultrasonic waves.
Magnetic Particle Inspection
At H2AIM, we employ this non-destructive testing strategy to detect surface and shallow subsurface discontinuities in ferromagnetic materials like iron, nickel, cobalt, and some of their alloys.
Long Range Ultrasonic Testing
H2AIM usually implements this non-destructive technique to analyze large volumes of material from a single test point.
Magnetic Flux Leakage
We commonly utilize this non-destructive testing method to identify corrosion and pitting in steel structures like pipelines and storage tanks.
Ultrasonic Thickness Gauging
We use this particular procedure that comprises conducting non-destructive gauging of the local thickness of a solid substance, including pipes, boiler tubes, plates, etc.
Time of Flight Deflection
We use Time of Flight Deflection – a specially designed non-destructive testing method – for finding flaws in welds.
Phased Array Ultrasonic Testing
This is one of the common methods used by H2AIM for wall thickness measurement, defect detection and corrosion testing. It is an advanced process of ultrasonic testing that has many applications in medical imaging and industrial nondestructive testing.
Radiographic Testing
H2AIM is an expert in conducting Radiographic Testing – a non-destructive examination that incorporates the use of either x-rays or gamma rays – to check non-uniform materials.